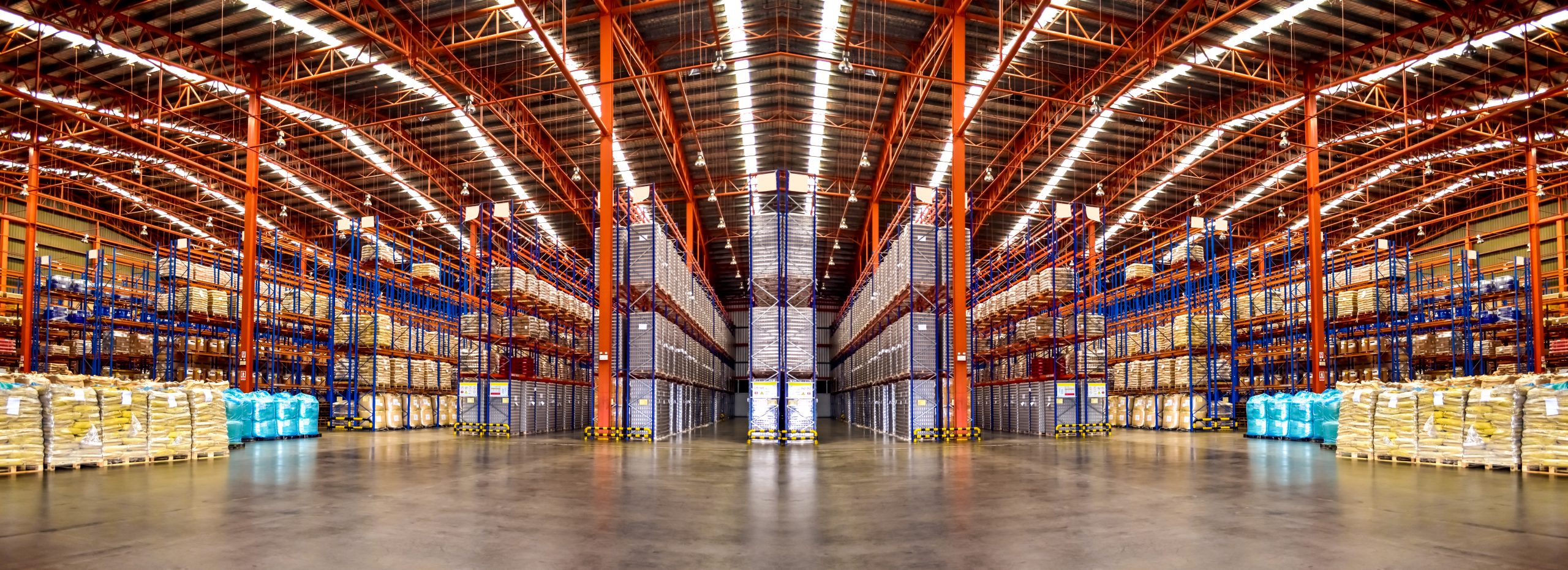
Warehousing plays a pivotal role in the intricate web of supply chain logistics. As businesses strive for greater efficiency and cost-effectiveness, the evolution of warehousing has become a cornerstone of successful operations. From inventory management to the integration of cutting-edge technology, the impact of strategic warehouse operations cannot be overstated.
Evolution of Warehousing in Logistics
The evolution of warehousing in logistics has revolutionized the storage and distribution of goods, significantly impacting supply chain efficiency. Historically, warehouses were perceived as mere storage facilities. However, with technological advancements and globalization, the role of warehouses has transformed into sophisticated centers for inventory management, order processing, and value-added services. This evolution has been driven by the need for improved speed, accuracy, and flexibility in meeting customer demands.
Warehousing has evolved from traditional, labor-intensive operations to highly automated facilities equipped with advanced technologies such as robotics, IoT, and warehouse management systems. These technologies have enabled real-time inventory tracking, efficient order fulfillment, and seamless integration with transportation networks, leading to reduced lead times and optimized resource utilization.
The concept of shared warehousing and distribution centers has gained prominence, allowing multiple organizations to benefit from cost savings and enhanced operational synergies. This evolution has not only improved the overall efficiency of supply chains but has also fostered a sense of belonging within the logistics community, as companies collaborate to utilize shared resources for mutual benefit. As warehousing continues to evolve, it is essential for businesses to adapt and embrace these advancements to remain competitive in the dynamic global marketplace.
Importance of Inventory Management
Inventory management’s significance in warehousing and supply chain logistics cannot be overstated. Effective inventory management is crucial for streamlining operations, reducing costs, and ensuring customer satisfaction. Here are four key reasons why inventory management is essential in the context of warehousing and supply chain logistics:
- Optimizing Stock Levels: Proper inventory management allows businesses to maintain optimal stock levels, preventing stockouts and overstock situations. This ensures that customer demand is consistently met while minimizing carrying costs and the risk of obsolete inventory.
- Enhancing Operational Efficiency: Efficient inventory management processes, such as accurate demand forecasting and real-time tracking, contribute to streamlined operations. This leads to improved order fulfillment, reduced lead times, and ultimately, enhanced customer service.
- Cost Control: Effective inventory management helps control costs associated with excess inventory, storage, and carrying expenses. By accurately monitoring inventory levels and turnover rates, businesses can minimize holding costs and free up working capital.
- Minimizing Risks: Inventory management mitigates the risks of stockouts, overstocking, and product obsolescence, thereby safeguarding the supply chain from disruptions and financial losses.
These factors underscore the pivotal role of inventory management in optimizing warehousing and supply chain logistics.
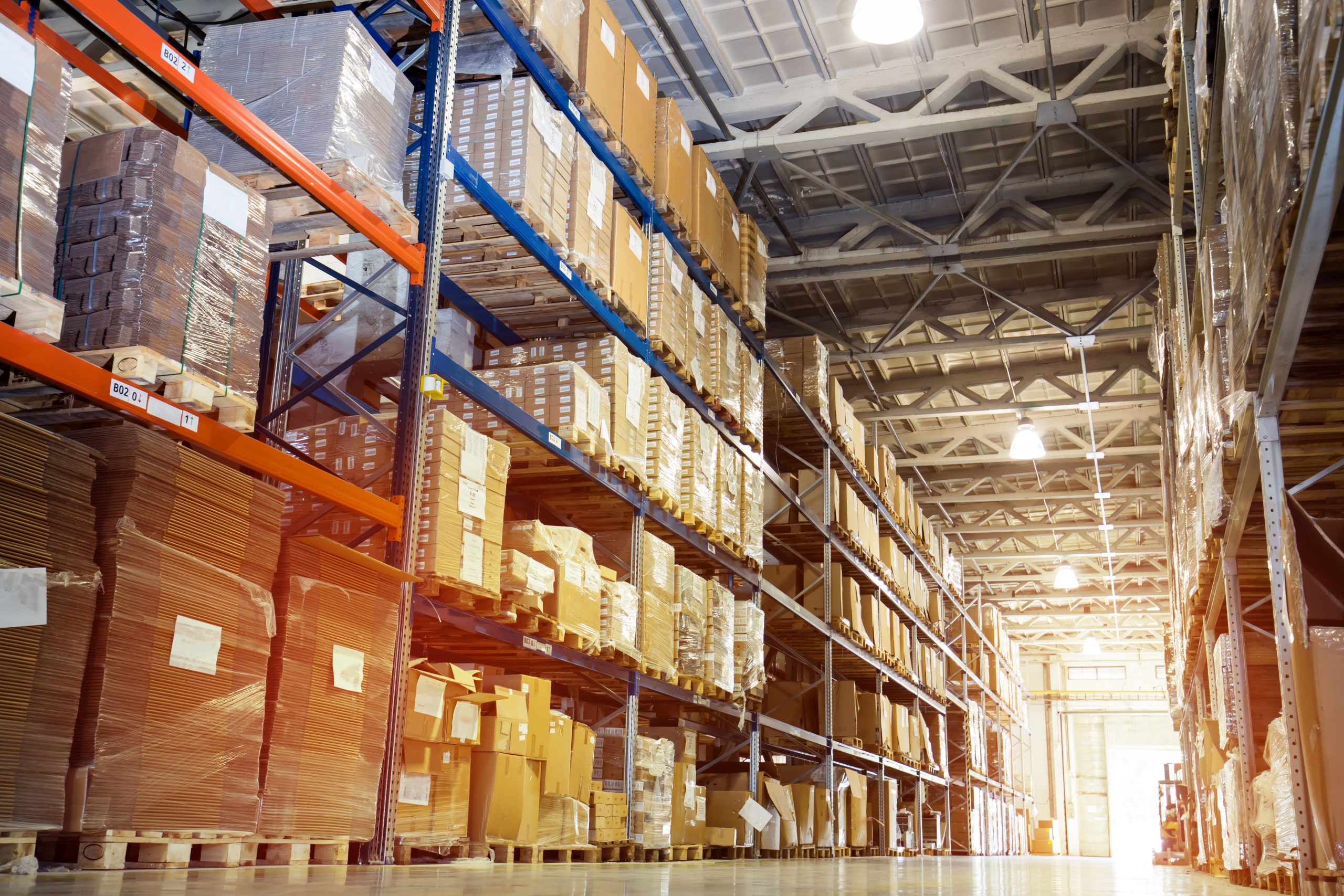
Role of Technology in Warehouse Operations
How can technology revolutionize and optimize warehouse operations within the context of supply chain logistics? The role of technology in warehouse operations is paramount in enhancing efficiency, accuracy, and overall productivity. With the integration of advanced warehouse management systems (WMS), businesses can streamline their operations through automation, real-time tracking, and data analytics.
WMS software enables better inventory control, precise order fulfillment, and seamless communication between different stages of the supply chain. Furthermore, the implementation of technologies such as RFID (Radio Frequency Identification), IoT (Internet of Things), and automated material handling equipment like conveyor systems and robotic arms, significantly improves the speed and precision of tasks within the warehouse.
Moreover, the use of technology in warehouse operations facilitates better demand forecasting, inventory optimization, and use of space. Through the use of data analytics and machine learning algorithms, warehouses can make data-driven decisions to optimize their layout, storage methods, and resource allocation. Additionally, technologies such as warehouse robotics and autonomous vehicles not only enhance operational efficiency but also contribute to a safer working environment for warehouse personnel.
Optimizing Warehouse Layout and Design
Optimizing warehouse layout and design frequently involves meticulous planning and strategic utilization of available space to enhance operational efficiency and productivity within supply chain logistics. A well-designed warehouse layout can significantly impact the overall performance of the facility, leading to smoother operations and improved customer satisfaction. Here are four key considerations for optimizing warehouse layout and design:
- Maximizing Space: Efficient space use is crucial for accommodating inventory and facilitating smooth material flow. Utilizing vertical space with mezzanines or high stacking, and implementing narrow aisle racking systems can optimize storage capacity.
- Logical Flow: Designing a layout that ensures a logical flow of goods from receiving to shipping can minimize travel time and streamline operations. This involves strategically placing different functional areas such as receiving, storage, picking, and packing to minimize unnecessary movement.
- Technology Integration: Incorporating advanced warehouse management systems, barcode scanning, and automation technologies can enhance accuracy, speed, and overall efficiency in warehouse operations.
- Flexibility and Scalability: A well-designed warehouse layout should allow for adaptability to meet changing business needs and future growth. Modular designs and flexible storage solutions enable easy reconfiguration as requirements evolve.
Enhancing Logistics Efficiency Through Warehousing
Enhancing logistics efficiency through warehousing involves strategic management of inventory flow and storage to streamline operations and minimize costs. By implementing advanced technologies such as warehouse management systems (WMS) and automated storage and retrieval systems (AS/RS), businesses can optimize their warehousing processes.
These systems enable real-time tracking of inventory, efficient order picking, and accurate demand forecasting, resulting in reduced lead times and improved customer satisfaction. Additionally, the adoption of lean principles within warehousing operations, such as just-in-time inventory management and continuous process improvement, contributes to enhanced efficiency.
Furthermore, effective space utilization and layout optimization contribute significantly to logistics efficiency. Using efficient storage methods like vertical racking and cross-docking can boost productivity by minimizing travel distance in the warehouse. Strategically placing warehouses near suppliers, manufacturers, and customers can shorten transportation routes, saving fuel and money. By leveraging these strategies, businesses can create agile and responsive supply chains, improving their competitive edge in the market.